Engineering bolts are used to hold parts together by applying a clamping force. When a bolt is tightened, it generates axial force that acts between the head and what it’s screwed into (usually a nut).
To get this force to create a good clamping joint several factors need to be considered including the tensile strength of the bolt body and its diameter. Other important factors are the material, thread, and preload.
Bolts can be made from a variety of materials depending on the type and strength required for a particular application. Carbon steel is commonly used because it offers good tensile strength and is relatively affordable. It can be strengthened by adding alloys such as chromium, molybdenum, nickel or vanadium. This process is known as hot-forging.
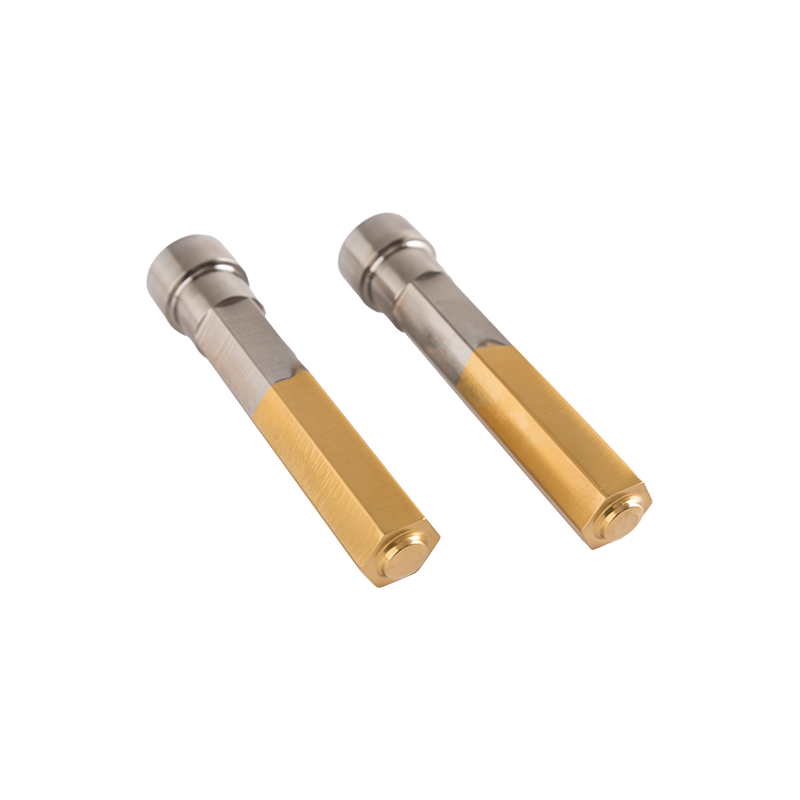
Alloy steels offer higher tensile strength than carbon steel and can withstand more demanding applications. They are often plated or hardened to increase their strength and improve their corrosion resistance.
Stainless steel bolts are typically used in applications where there is an issue with moisture or harsh environments. They are also easy to fabricate and provide hygienic properties. Other metals and alloys that can be used include brass, bronze or aluminum which are often chosen for their aesthetic qualities. They also offer good corrosion resistance but lack the strength of carbon steel fasteners. They may be plated or painted to further enhance their appearance.
Thread
While you may think of bolts in the very simple way that they hold stuff, there’s a lot more to them than meets the eye. And if you’re the type to delve into engineering nerdom, there are even more things to consider.
One big consideration is thread length, which relates to the amount of force that is transferred from the bolt head to the thread (and ultimately the load). This factor can be significant in determining whether a specific size bolt is able to be used in a particular application.
Another thing to consider is the thread’s pitch. This is the distance between adjacent thread peaks. Different thread pitches have different tensile stress areas, and this can make a difference in whether or not a bolt is suitable for an application. It also affects how easy it is to use and inspect a bolt. Fortunately, there are standard measurements for threads that are very helpful.
When threaded into a hole, bolts and nuts apply a clamping force that tries to squeeze parts together. To withstand this load, they must have a sufficient diameter and strength to meet the requirements of the application.
The length of the thread is determined by its major and minor diameters, along with the pitch (axial distance between adjacent crests). Industry standards require that the major diameter be smaller than the minor and that a bolt's grip length is equal to or greater than the sum of the thread depth and shaft diameter.
The first number in a bolt's designation indicates its nominal diameter, while the second number gives the number of threads per inch. Bolt sizes that are less than 1 inches can have one or two possible TPI configurations; larger bolts can have up to three. When a bolt is gradually loaded, there comes a point when it begins to yield, or permanently stretch, and eventually breaks. This is called the proof load.
Preload
When a bolted joint is preloaded it is clamped by a force Fp, and the connection and bolt are deflected by an additional force Fe which tends to separate the joint. If the total force of the separation force is less than or equal to the preload, then equilibrium exists.
A bolt preload is the amount of force applied to the bolt that is sufficient to prevent slip of the nut and head. The preload is based on the bolt-shank strength and is usually above the strain point of failure.
The calculation of the preload is a nonlinear problem. This adds to the complexity of a model, especially when the shear and axial loads are combined. The calculation is also sensitive to the contact properties used. For example, tangential or penalty friction may be used for the contact between the bolt-shank and the plate elements. Moreover, differences in mechanical properties between the bolt and flange materials can cause changes in the preload.